The aspiration for an iPhone bearing a ‘Made in the USA’ label is a recurring theme in American political discourse, yet the practical hurdles remain as formidable today as when the late Steve Jobs bluntly dismissed the idea to President Barack Obama over a decade ago.
While the occupants of the White House and Apple’s corner office have changed, the complex realities of global manufacturing continue to challenge the ambition.
Following the imposition of steep “reciprocal tariffs,” the Trump administration has reiterated its belief that the US possesses the workforce and resources to build iPhones domestically.
However, neither Apple CEO Tim Cook nor the tech giant itself has publicly endorsed this vision.
Instead, industry analysts paint a picture where shifting iPhone production stateside ranges from prohibitively expensive to outright impossible.
The price of patriotism: sticker shock for a US-made iPhone
Estimating the cost of such a theoretical shift yields sobering figures.
Wamsi Mohan, an analyst at Bank of America Securities, calculated in a recent note that labor costs alone could inflate the price of an iPhone 16 Pro (currently $1,199) by 25%, pushing it towards the $1,500 mark.
Wedbush analyst Dan Ives offered an even starker projection shortly after the latest tariff announcement, pegging a potential US-made iPhone at $3,500.
His estimate factored in a hypothetical $30 billion investment over three years needed just to move 10% of Apple’s supply chain to the US.
This financial chasm reflects Apple’s deep integration with global, particularly Chinese, manufacturing.
Currently, over 80% of Apple’s products are made in China, goods now subject to a hefty 145% import tariff under the new rules.
Experts universally agree that relocating this intricate network faces immense challenges, making the prospect highly unlikely in the near term.
“I don’t think that’s a thing,” quipped Needham’s Laura Martin on CNBC, echoing Wall Street’s long-held skepticism.
Jeff Fieldhack, research director at Counterpoint Research, was more direct: “It’s just not a reality that on the time frame of imposing tariffs that this is going to shift manufacturing here. It’s pie in the sky.”
Beyond borders: the intricate web of global manufacturing
Apple, while designing its products in California, relies heavily on contract manufacturers like its top supplier, Foxconn.
Replicating Foxconn’s massive, highly efficient Chinese operations in the US presents multiple obstacles.
Even securing a partner willing to build US assembly plants would require years of construction and investment, all under the shadow of potentially shifting trade policies that could render such facilities economically unviable.
The most significant hurdle, however, lies in the workforce.
The Trump administration views the potential for mass employment as an attraction, with Commerce Secretary Howard Lutnick envisioning “the army of millions and millions of human beings screwing in little screws to make iPhones” migrating to America.
Yet, the scale and nature of the labor force required clash with US realities.
The human equation: labor costs, scale, and skills divide
Foxconn operates vast campuses in China, complete with worker dormitories and transport, enabling rapid scaling of its workforce, often drawing temporary labor from surrounding regions.
This system allows employment to surge seasonally – crucial for meeting the intense demand preceding new iPhone launches each fall – helping Apple produce over 200 million units annually.
Last fall, Foxconn reportedly hired 50,000 extra workers at just one factory for the iPhone 16 ramp-up.
This operational model, however, has faced scrutiny over working conditions, including grueling hours and pressure for overtime, highlighted tragically by worker suicides in 2011 that led to safety nets being installed around buildings.
Crucially, the cost of labor differs dramatically. During the iPhone 16 surge, the reported hourly wage in China was 26 yuan ($3.63), plus a signing bonus equating to roughly $1,000.
In contrast, California’s minimum wage stands at $16.50 per hour.
Bank of America’s Mohan estimated US-based assembly and testing labor would cost $200 per iPhone, compared to $40 in China.
Beyond cost and scale, Apple CEO Tim Cook has previously cited a skills gap.
In a 2017 interview, Cook lamented the lack of sufficient tooling engineers in the US – specialists essential for translating complex digital designs into physical manufacturing processes.
He illustrated the disparity starkly: a meeting of such engineers in China could fill “multiple football fields,” while gathering enough in the US would struggle to fill one.
“The reason is because of the quantity of skill in one location, and the type of skill it is,” Cook explained regarding Apple’s China production footprint.
Echoes of ambition: lessons from Wisconsin and beyond
Recent history offers cautionary tales. A high-profile 2017 announcement by Foxconn, championed by Trump, promised a $10 billion investment and 13,000 jobs for advanced manufacturing plants in Wisconsin.
Though Apple was never officially linked, Trump claimed Apple would build “big beautiful plants.”
The project ultimately faltered, scaled back dramatically, producing face masks during the pandemic instead of electronics, and created only a fraction (1,454) of the promised jobs. Most of the facility remains unbuilt.
Apple and Foxconn did successfully expand iPhone production to Brazil in 2011, primarily to circumvent high import duties there.
While that plant operates today, it highlights another challenge: even with local assembly, most components were still imported from Asia.
Four years after its announcement, Brazil-made iPhones reportedly retailed for double the price of their Chinese-made counterparts.
A more positive, albeit limited, example exists with Taiwan Semiconductor Manufacturing Co. (TSMC), Apple’s main chip supplier.
TSMC recently began producing small quantities of advanced chips at a new factory in Arizona, with Apple as a key customer, demonstrating that some high-tech manufacturing can be established in the US, though it remains a complex and costly endeavor.
A global jigsaw: the challenge of sourcing components
Even if final assembly were feasible in the US, the iPhone itself is a global product.
Key components originate worldwide: processors from TSMC in Taiwan, displays from South Korean firms like LG or Samsung, and countless other parts predominantly from China.
Under current tariff structures, Apple would likely face duties on these imported components (though semiconductors are currently exempt), further inflating costs unless specific waivers could be secured.
Mohan calculated that if the recent 90-day tariff pause expires, the combined impact of tariffs and higher labor costs could increase an iPhone 16 Pro Max’s price by a staggering 91%.
“While it may be possible to move final assembly to the US, moving the entire iPhone supply chain would be a much bigger undertaking and would likely take many years, if even possible,” Mohan concluded.
Faced with these realities, Tim Cook has adopted a different approach than Steve Jobs’ outright dismissal.
Cook has actively engaged with the Trump administration, attending events and highlighting Apple’s significant domestic investments (a cited $500 billion commitment, including AI server production in Houston), which Trump often references approvingly.
This strategy proved effective during Trump’s first term, securing temporary tariff exemptions for key Apple products like the iPhone.
A notable moment came in 2019 when Apple committed to assembling its high-end ($3,000) Mac Pro computers at a Texas facility, culminating in a factory tour attended by both Cook and Trump.
Analysts suggest Apple might employ similar tactics now, potentially committing to small-scale US production of lower-volume items like HomePods or AirTags as a political gesture to gain broader exemptions.
Erik Woodring of Morgan Stanley told CNBC, “Given we now know that the Trump administration is willing to negotiate, we wouldn’t be surprised to see Apple commit to some small-volume production in the US… to try and win an exemption.”
Ultimately, while the call for a ‘Made in the USA’ iPhone resonates politically, the intricate tapestry of global supply chains, labor economics, and specialized skills presents monumental barriers.
Apple’s path forward likely involves continued political navigation rather than a fundamental, and costly, shift in its manufacturing geography.
The post Want US-made iPhone? Prepare your wallet for a major price hike appeared first on Invezz
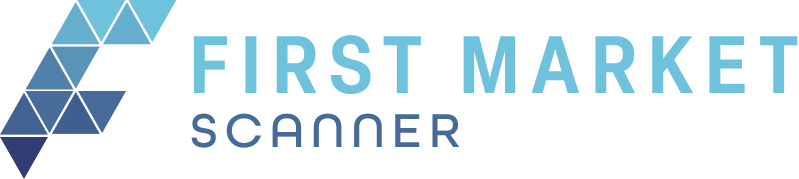